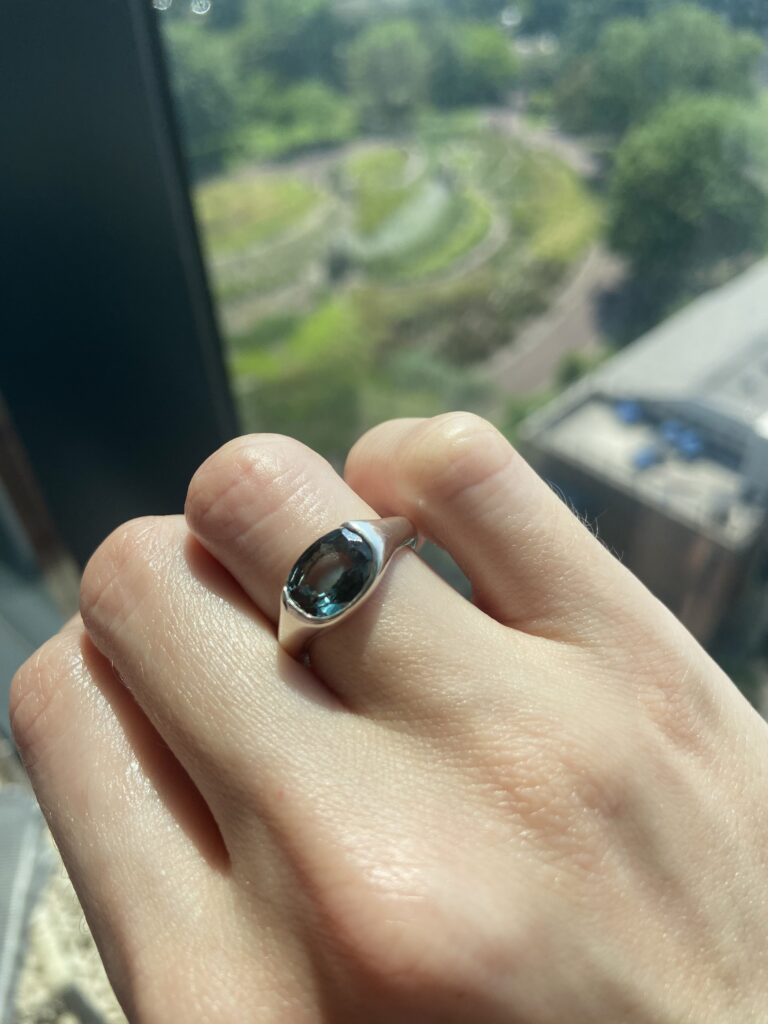
My friend Griffin recently sent me a text explaining how he modeled a copy of an expensive ring in Blender and sent the mesh file to a casting company who had it cast in sterling silver all for under $35. I couldn’t help but become obsessed with that project. I immediately asked my girlfriend Kari to find a ring that she wanted and showed her what Griffin had made. She luckily already had a ring she had found on Pinterest which was a gold band with a green sapphire and retailed for $8000.
We found a similarly sized (2.1 carat) sapphire on Ebay for $29 shipped which we purchased, as soon as it arrived I measured it and made a model in Fusion 360. With the CAD model of the gem I was now able to start designing the ring. I measured her finger and made a rough model of the ring, used the gem as a cutting tool to create a negative cavity for it and expanded this cavity to give it some room, created some prongs so that I could later set the stone in its cavity and then smoothed all surfaces and edges.
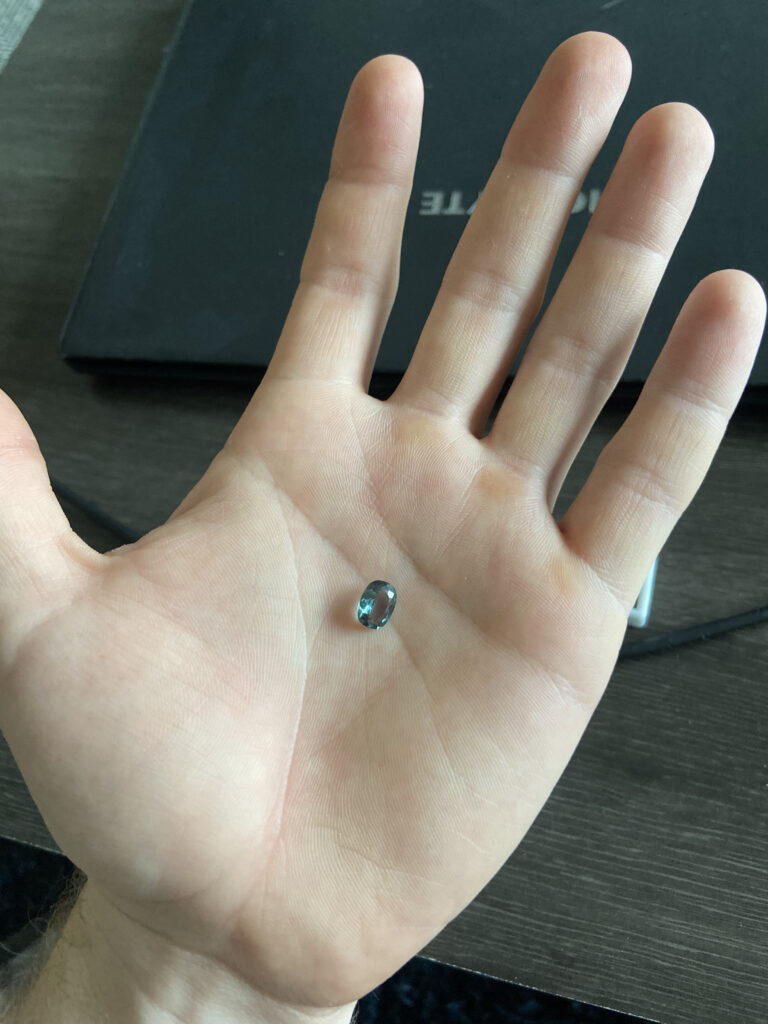
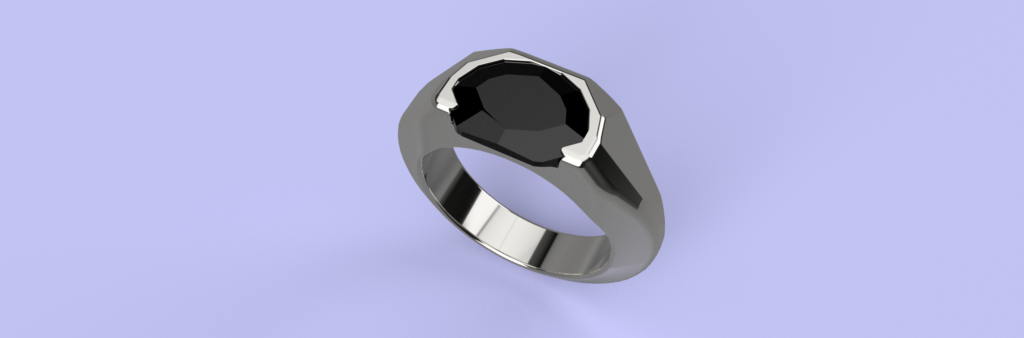
I uploaded this model to Craftcloud and settled on a solid sterling silver quote for $26.88. It took a couple weeks to arrive and was quite rough looking but the gem fit perfectly.
We set the stone by using a hammer and punches to bend the prong/tabs I had designed into the ring over the sapphire, rough polished and tried it on.
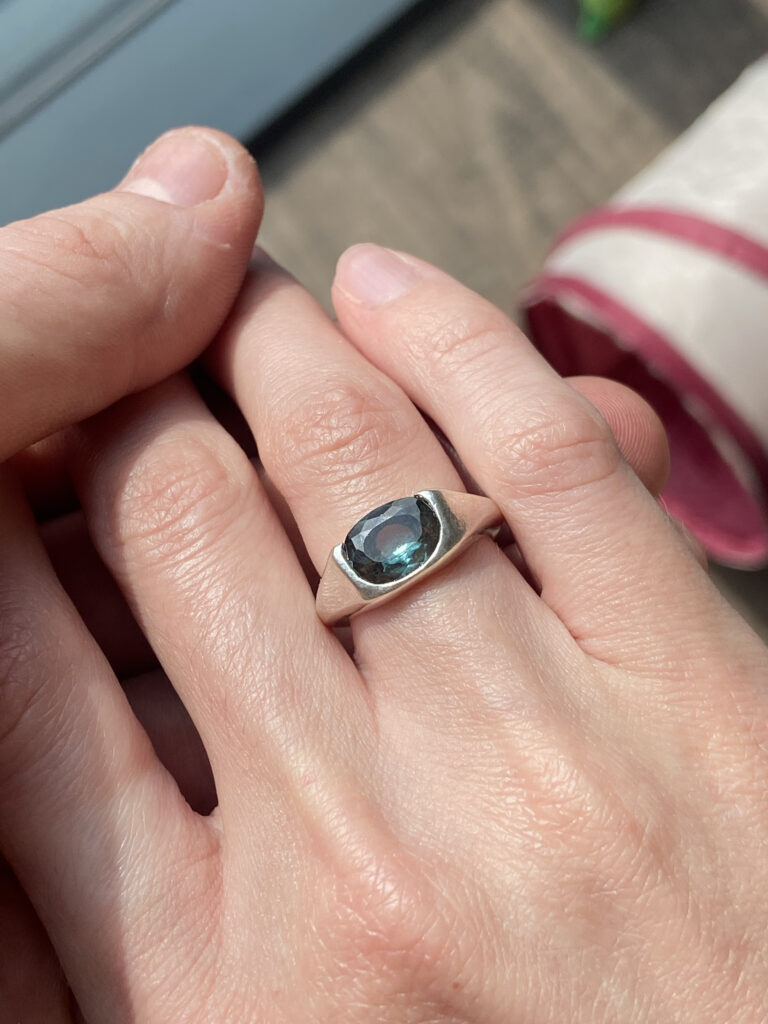
We were both really happy with how it was turning out but we both knew it wasn’t perfect. It did not look like the ring we were basing our design on and it was too bulky looking for her hand. We hand filed the silver away for hours, using metal files, nail files and then back to polishing compound and this time we ordered a 50,000 grit finishing polishing compound to really shine the silver.
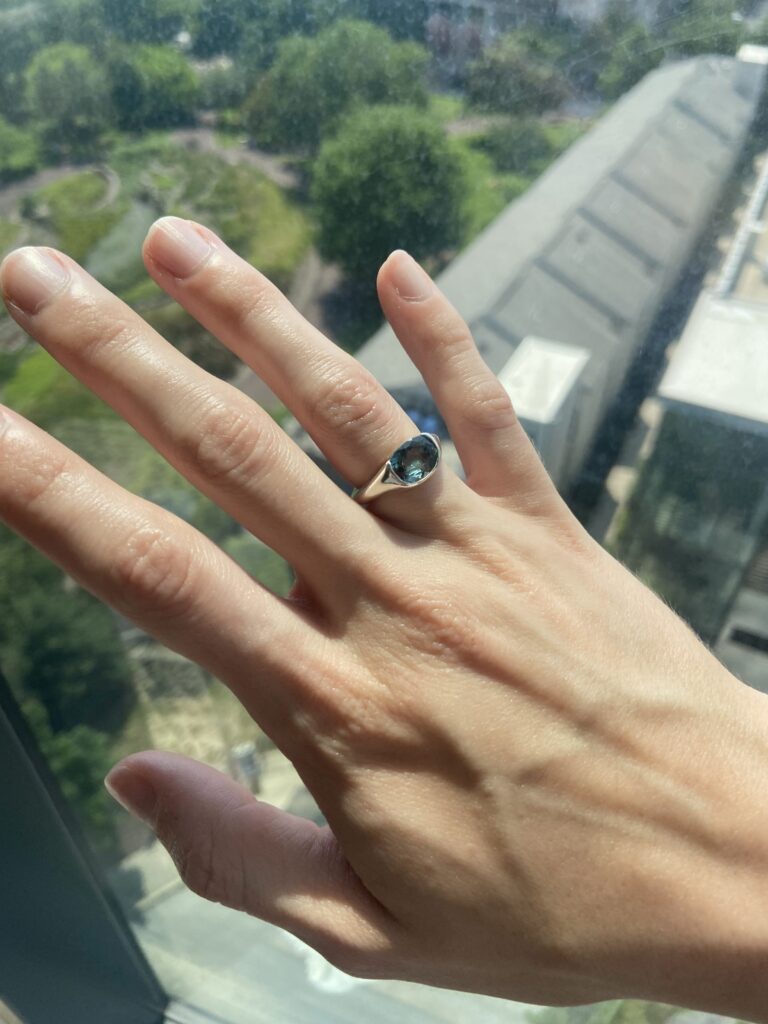
This time it was as perfect as we could get it without re designing the ring. We are both very happy with how it turned out but there’s a few things I would change if I ever make another. The prongs were larger than they needed to be which made securing the stone very difficult, the shape of the ring wasn’t right because I was struggling to achieve the desired shape in Fusion360 (Blender would have been better), and the design for where the stone enters the ring was larger than it needed to be causing a gap when all said and done.
Check out the video below for the entire build process